大家好,我是一颗电芯。准确来说,是一颗即将被安装到轩逸·纯电上的电芯。
不久之前,我的“爸爸”——东风日产,向我的“妈妈”——宁德时代下了一份“私人订制”的订单。
没过多久,我就和我千千万万的兄弟们一同,来到了这个世界上。
宁德时代的工厂很先进,但当我再一睁眼,我已经发现自己躺在广州花都东风日产第二工厂的生产线上。
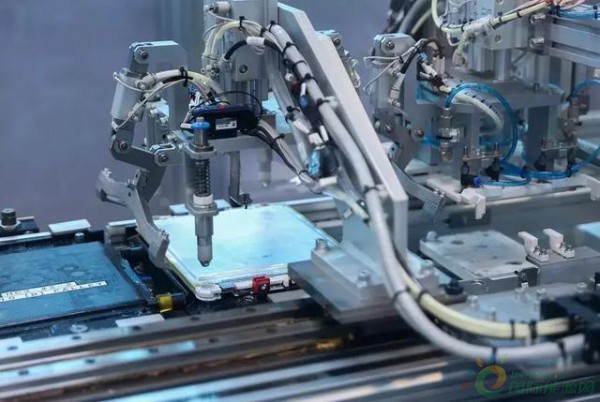
而围绕在我身边的,还有来自全国的专业汽车媒体老师们。
听说,我今天将要经历一趟“冒险”之旅,完成从一颗电芯(CELL),到成为一个电池模块(MODULE),再到成为一个电池组(PACK),最后成为一辆轩逸·纯电的蜕变。
可能大家还不知道,轩逸·纯电,是合资品牌的首款国产
纯电动汽车。
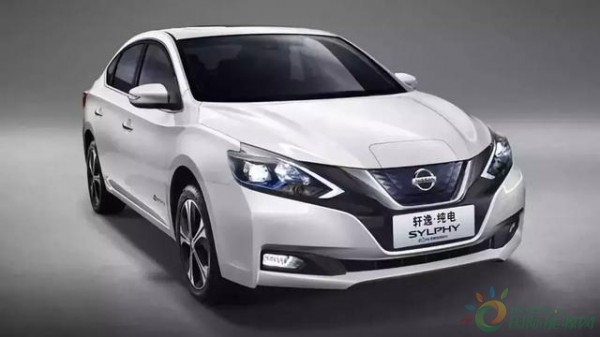
他采用与日产聆风LEAF相同的专业纯电平台打造。
更继承了LEAF累计销量43万台、累计行驶里程100亿公里,而电池0重大事故的优秀基因。
得知自己要变成他的一份子,眼前这个陌生的环境,似乎也变得可爱起来。
那么,我从一块电芯到一辆完整的电动车到底要经历些什么?
下面,我们就来一同开始这场“冒险”吧。
1
按照工程师的说法,我和兄弟们,最先要经历的第一个流程,就是完成从CELL(电池单元)到MODULE(电池模块)的生产过程。
我们完成这一过程的地方,更堪称是顶尖工艺的集结地。自动化率高达96%!
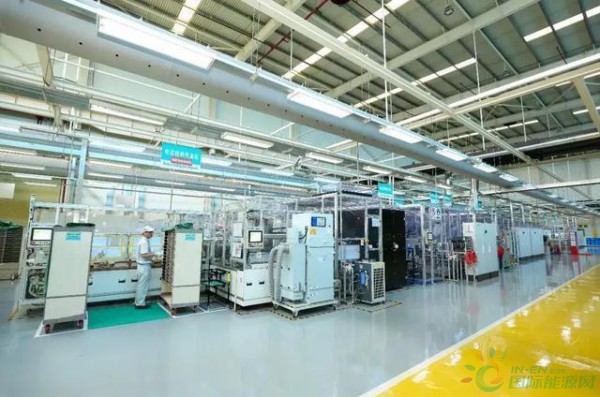
此刻,我正身处数千平米的生产线,被两排精密的全自动生产设备占据了绝大部分空间。
但我却只看到了屈指可数的数个工作人员穿梭其中。
整条生产线仿佛让人走进了“外科手术室”般,在干净、整洁的同时,给人精密、先进的第一印象。
而我和我的兄弟们,还都要经历12道工艺流程、14项品质检查及198项生产管控环节。
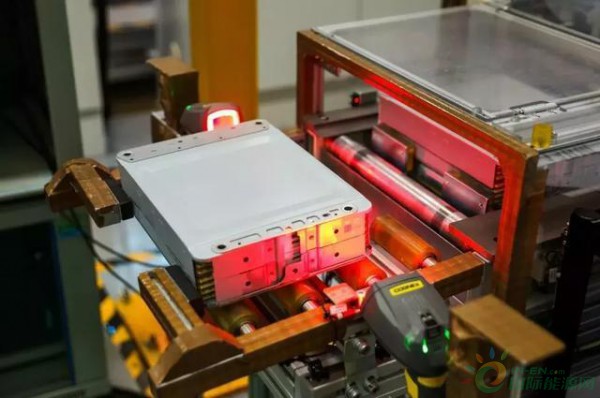
其中,更包括了激光裁剪、超声波焊接、热熔胶注塑、激光打码等多道精密自动化生产工序。
最终,在走完这些工序后,我们便组合成了一个完整的MODULE(电池模块)。
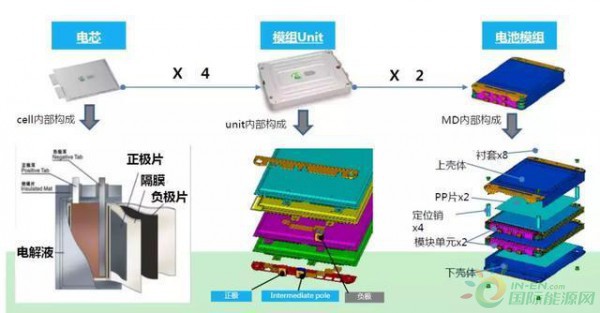
2
完成MODULE后,我的这场“冒险”只是走完了第一步。
接下来,更多和我一样的兄弟们将加入进来,并组成一个PACK(电池组)。而一个完整的PACK,才是轩逸·纯电的动力来源。
.jpg)
这个过程,离不开那些全副武装,身穿戴着绝缘鞋、绝缘手套、安全头盔、护目镜的工作人员们对我们的悉心“照顾”。
听东风日产的工程师介绍,这里的每个工作人员除了持有国家认证的电工资格证书外,还拥有非常丰富的高压作业经验。
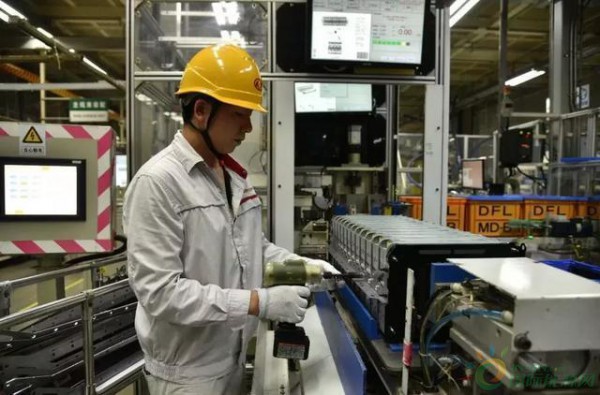
毕竟,24个电池模块串联后电压高达380伏,专业事必须专业人来做。
电池组的组装过程要经过堆栈分装、主线束装配、高压检查、合盖检查、气密测试、充电测试、以及QA检查等6道主要工序。
为了确保整个生产流程的完全可控,我们“上头”还有一个叫做MES的系统扮演着“天眼”的角色,事无巨细地记录着每个生产的细节。
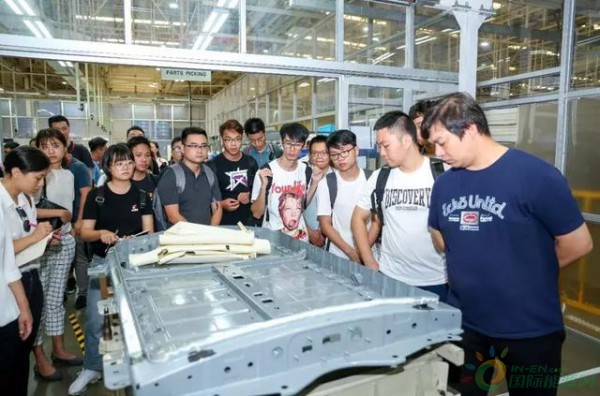
定值无线电枪正在紧固的螺丝的位置、力矩、当班员工的编号、生产的时间……所有一切都被清晰地计入系统,悉数上传至日产总部,其中重要数据更是要保存5年以上。
当然,即便我们组成了一个PACK,但远还不到可以组装“上车”的时候。
东风日产为了严格确保电池品质。我们整个电池包的关键参数需要进行校验,确保PACK符合设计要求的同时,避免虚接等情况发生。
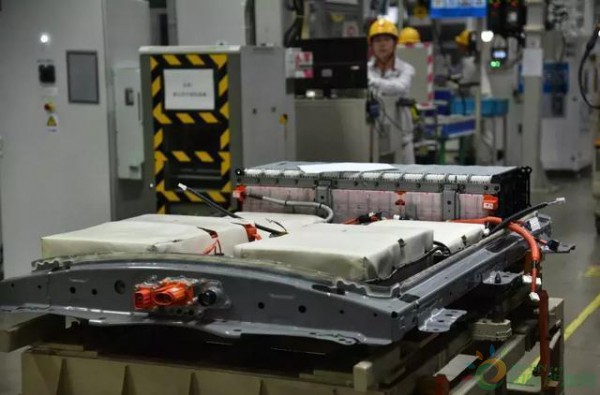
1.5KPa的高压气体被注入到被密封好的我们的包内,并要求在15秒内没有气体外泄,以确保整个电池包处于完全密封的状态。
最后,我们还有接受15分钟高压充电测试,模拟21种日常容易遇到的充电情境。
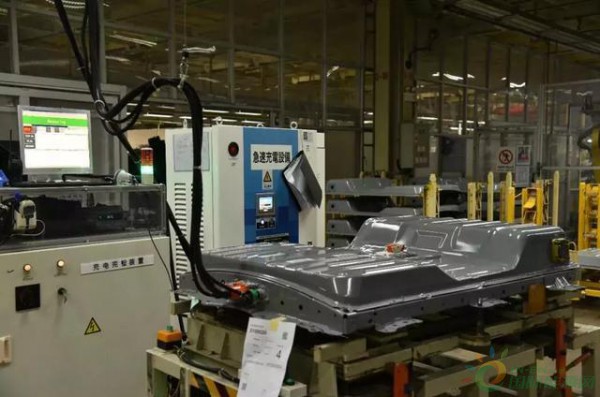
并且,还有专门的QA检测环节。对整个生产装配流程再次进行校验,确保所有环节均按照设计要求进行生产和检测,实现过程、检查和下线每道工序都达到100%的品质。
3
最后当然就是总装“上车”的环节了。
轩逸·纯电要经历的总装过程其实也和许多燃油车型也是大同小异,括的车身和底盘的结合,还有电池、电驱模组的安装等等。
但重点值得一说的是,东风日产还考虑到了实际用车过程中,环境因素变化对我们的影响,制定了非常周密的安全防御设计。
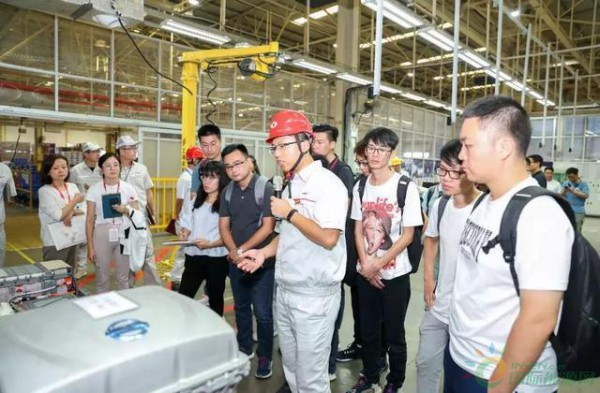
为了防止机械变形、挤压、撕裂、隔膜破裂导致的内短路,日产克制地将我们布置在前后轮中间,并且采用了1.2GPa超高强度装甲。
我们内部还有玻璃纤维和凯夫拉组成的隔热材料进一步防护,更有极端情况下能够迅速释放内部压力的泄压阀。
此外,我们周围还留出足够的防碰撞溃缩空间,最大限度提供被动安全保障。
同时,为了防止过充、老化、低温对我的影响,日产LEAF做了大量的数据积累和实验,定义出明确清晰的充电电流电压边界,以此管控整个充电过程,保障充电的安全。
功夫拍案
经历完这一整场完整的“冒险”,我发现, 与其说是“冒险”,还不如说是东风日产从源头开始,将所有可能出现的风险都降到了最低。
也正是因为东风日产为了轩逸·纯电乘客的安全做了那么多不易被察觉的努力。
拥有日产聆风100亿公里,电池0重大事故优秀基因基因的轩逸·纯电,无愧于纯电领域的安全标杆。